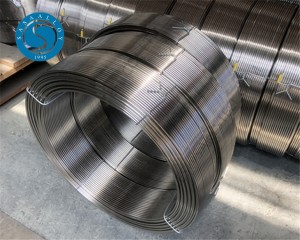
Inconel X-750 is a precipitation-hardenable nickel-chromium alloy renowned for its exceptional mechanical strength and oxidation resistance at high temperatures. Commonly used in aerospace, nuclear, and industrial gas turbine applications, this alloy exhibits excellent corrosion resistance, stress-rupture strength, and thermal stability. However, welding Inconel X-750 presents unique challenges that must be managed to preserve the alloy's integrity and performance.
1. Welding Characteristics of Inconel X-750
Due to its precipitation-hardening nature and high nickel content, Inconel X-750 is generally considered to have moderate to difficult weldability. Key considerations include:
• Hot cracking susceptibility: Particularly in the heat-affected zone (HAZ), especially if improper filler materials or welding parameters are used.
• Loss of mechanical properties: Precipitation-hardened alloys may suffer from degradation of strength near the weld due to thermal cycling.
• Post-weld heat treatment (PWHT) is often required to restore desired mechanical properties.
2. Recommended Welding Methods
The preferred welding methods for Inconel X-750 include:
• GTAW (TIG Welding): Offers precise control and is widely used for small components and thin sections.
• GMAW (MIG Welding): Suitable for higher deposition rates and larger structures.
• Electron Beam and Laser Welding: Employed in high-precision applications.
3. Filler Metal Selection
For most applications, Inconel filler metals such as ERNiCr-3 or ERNiCrCoMo-1 are recommended. Selection depends on service temperature and corrosion requirements. It is critical to match the thermal expansion and chemistry to reduce residual stresses and avoid cracking.
4. Pre-Weld Preparation
1.Cleanliness: Remove all oxides, oils, and surface contaminants prior to welding.
2.Joint design: Use designs that minimize restraint and reduce the risk of hot cracking.
3.Control of interpass temperature: Maintain moderate interpass temperatures to avoid excessive heat buildup.
5. Post-Weld Heat Treatment (PWHT)
A common PWHT for Inconel X-750 is:
• Solution annealing at ~980°C (1800°F) followed by rapid cooling.
• Aging treatment around 705°C (1300°F) for precipitation hardening.
This treatment is essential to regain high-temperature strength and stress-rupture performance.
6. Applications Requiring Welded Inconel X-750 Components
• Jet engine components (seals, springs, turbine blades)
• Nuclear reactors (core holders, springs)
• High-temperature bolting and fasteners
• Heat exchanger tubes in severe environments
Conclusion
Welding Inconel X-750 demands careful control over process parameters, filler selection, and post-weld treatments. When executed properly, welded joints can retain excellent mechanical properties and corrosion resistance, even under extreme conditions. Whether for aerospace or nuclear-grade components, understanding the weldability of Inconel X-750 ensures structural reliability and long-term performance.
Post time: May-20-2025